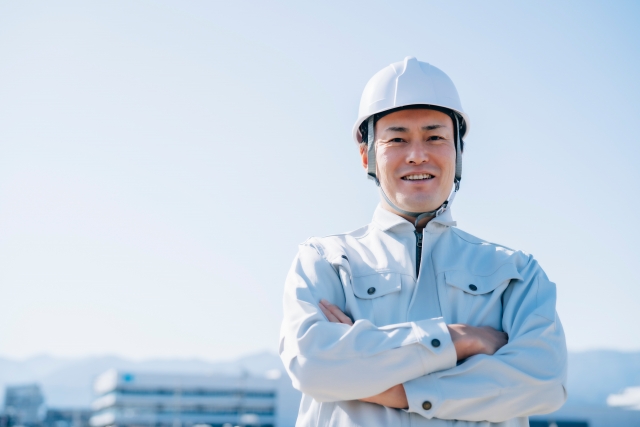
DX(デジタルトランスフォーメーション)に向けた取り組みは、テクノロジー企業を中心に始まり、今や、製造業にまで広がるようになりました。しかし、「なぜ取り組む必要があるのか」「どこから取り組めばいいのか」といった疑問をお抱えの担当者も多いのではないでしょうか。
そこでこの記事では、製造業におけるDXの現状や進め方について、イチから分かりやすく解説します。
なぜ、製造業においてもDXが重要なのか?
なぜ製造業においても、DXに向けた取り組みが重要なのでしょうか?その理由には、「製品が生み出す付加価値の低下」「少子高齢化による人手不足」などの問題が挙げられます。
近年では、加工・製造の低コスト化や、生産のグローバル化などによって、製品そのものの付加価値は下がりつつあります。製造業が競争の激しい市場で生き残るために、「いかに高い品質を保ちながら、低価格を実現するか」といったことが課題となっているのです。
また、日本では少子高齢化が進み、企業の人材確保が年々難しくなってきています。社内で高齢化が進み、新たな働き手がいなくなると、技術承継ができなくなる場面に遭遇するでしょう。
製造業がDX化を進めることで、製造の低コスト化や、人手不足の解消をはじめとしたメリットを期待できます。とくに、資金や人手を確保しにくい中小企業にとっては、喫緊の課題だといえるでしょう。
製造業のDX化によって実現できること
ここでは、製造業のDX化によって、どのようなことが実現できるのかについて説明します。
対象アプリケーションの画面を解析し、操作項目をUIオブジェクトとして認識して操作を行う方式
画面を画像として捉え、画像で操作項目を認識して操作を行う方式
画面内相対位置や矢印キーなどで操作項目の操作を行う方式
バリューチェーンの効率化
製造業のDX化を進めることで、バリューチェーンの情報を見える化し、スムーズな業務の流れを実現できます。従来の「勘」や「経験」に基づいた業務から、客観的な情報に基づく合理的な判断が可能になるのです。
とくにバリューチェーンにおいては、受発注情報の入力、出荷状況の記録、生産現場の情報収集など、定型的な業務が多く発生します。これらを、RPAや受発注システム、在庫管理システムなどによって管理することで、チェーン全体の流れをスムーズにできるのです。
製造業のバリューチェーンにおいて、DXは「潤滑油」のような役割を果たします。企業が取り組みを進めることで、受発注ミスの削減や、リードタイムの短縮などにつなげられるでしょう。
製品・サービスのスピーディーな開発・改善
製造業においてDXが浸透することで、製品やサービスの情報をリアルタイムで共有し、迅速な製品開発・改善ができるようになります。他社と比べた競争力強化にもつながるのがメリットです。
たとえば、顧客のクレームや要望といったデータは、営業やカスタマーサポートなど、特定の部門内にとどまっていることが多々あります。開発部門へ知らされるのは、月一回の報告会議のときだけ、といった事例も少なくありません。
また、開発部門で設計やシミュレーションがうまくいかず、製造部門への伝達が遅れてしまう、といった事例も考えられるでしょう。製造部門での生産量をはるかに超えた数で営業部門が受注してしまう、といったことも考えられます。
どの問題も、それぞれの業務が自部門だけで完結していることから発生しています。DXを進めることで、部門内に眠っている製品データや進捗状況がすべて共有されるので、より全体的な視野で業務を進められるようになるのです。
新しいビジネスモデルの発案
製造業がDXを進めることで、既存のビジネスを改善するだけでなく、新しいサービスの開発・提供にもつながるようなことがあります。
たとえば、小松製作所が開発した「KOMTRAX(コムトラックス)」がよい事例です。同社は、建設機械向けの、ネットワーク接続ができるセンサー装置を開発しました。
当初はオプションとしてセンサー装置を提供していましたが、人気の高まりを受けて、標準装備にすることを決定。機械設備のコンサルティングサービスも提供することで、新たなビジネスモデルを確立しました。
また、DXの一環で開発したソフトウェアが、製造業界のプラットフォームになるような事例もあります。「CADDi(キャディ)」と呼ばれる製造業向けの受発注プラットフォームがよい例です。
同社では、金属加工部品の加工を委託したい発注者向けに、独自のアルゴリズムを用いて、最適な加工会社を選定するサービスを提供しています。現在では、多くの製造業に利用されるプラットフォームへと成長しました。
上記の事例のように、製造業のDXには、さまざまなビジネスチャンスが広がっています。DX化へいち早く取り組むことで、新たなサービスの発案にもつながるでしょう。
製造業におけるDXの現状
では、製造業のDXはどれくらい進んでいるのでしょうか。富士通株式会社が発表した「グローバルデジタルトランスフォーメーション調査レポート2019」によると、業種別のDXの進捗は、以下の結果になりました。
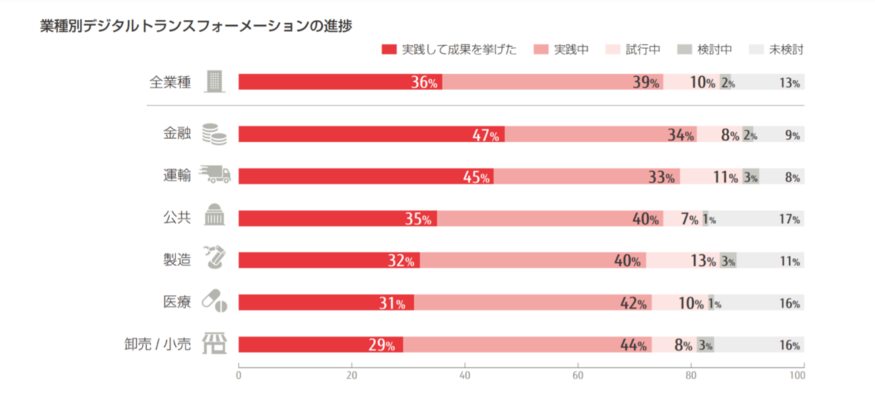
出典:富士通株式会社-グローバルデジタルトランスフォーメーション調査レポート2019
「実践して成果を挙げた」と答えた割合は32%で、金融や運輸といったほかの業種と比べて、やや遅れをとっているのが現状です。「試行中」「検討中」「未検討」と答えた割合が37%もあることを踏まえると、まだまだ改善の余地があるといえるでしょう。
製造業がDXを実現するための6つのステップ
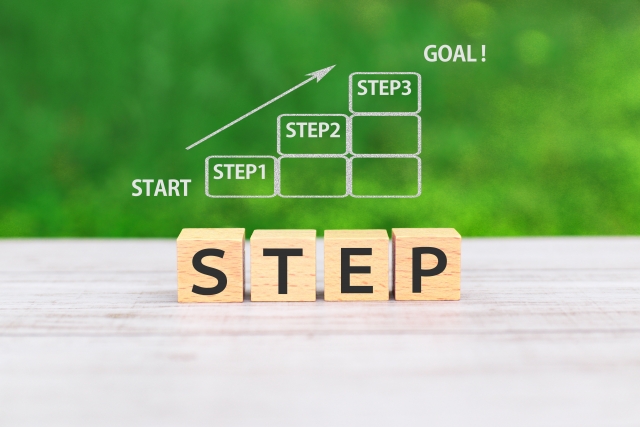
ここでは、製造業が実際にどのようにDXを進めればいいのかについて、6つのステップで解説します。「どこから手を付ければいいのか」とお悩みでしたら、ぜひ参考にしてください。
1.目的の明確化
まず、自社がどのような目的でDXを進めるのかを明確にしましょう。全体的な方向性が定まっていないと、プロジェクトが意図していない方向へ進んだり、現場での活用が進まなくなってしまったりするからです。
製造業におけるDXの目的には、「コスト削減」「業務の効率化」「社内における情報共有の促進」など、さまざまにあります。社員が一丸となって取り組めるように、分かりやすく具体的な目的を設定しましょう。
2.組織体制の整備
次に、DX化のプロジェクトを進めるための組織を整備していきます。
具体的には、社内で求心力を持つメンバーのほか、DXに関する専門知識を持ったメンバーが必要です。もし社内で人材を確保できなければ、外部から調達するのも一つの手でしょう。
組織体制を整備する際は、初めから大人数のチームにしないことが重要です。DXへの意識が高い少数のメンバーに限定することで、合意形成をスムーズに進められます。
3.DX化の現状把握
組織体制が整ったら、自社のDXに関する現状を把握しましょう。抱える課題や、ボトルネックを明らかにすることで、適したDX施策の実施が可能になるからです。
具体的には、以下のポイントをチェックしましょう。
- 機械設備のデータは取得できているか
- システム間のデータ連携は進んでいるか
- 部門間でスムーズに情報共有するための仕組みは整えられているか
- 作業は可能な限り標準化されているか
- 老朽化したシステムは存在しないか
課題となる部分を見つけ出したら、原因と対策を考えましょう。
たとえば、部門間での情報共有が進んでいない原因として、部門ごとに別々のコミュニケーションツールを使っていることが理由だとします。対策方法として挙げられるのは、どの部門でも統一して使えるコミュニケーションツールの導入です。
4.要件定義の実施
続いて、課題を解決するためのIT技術について、要件定義を実施していきます。要件定義とは、システムに必要な機能や性能、導入プロジェクトの進め方などを明文化していくことです。
自社だけで進めるのが難しい場合は、外部のコンサルティングサービスを活用したり、ITベンダーへ直接問い合わせてみたりするのがおすすめです。
要件定義をする際は、外部へ任せっきりにしないよう注意しましょう。自社の事情を一番よく知っているのは自社なので、あくまでも主体的に取り組む姿勢が大切です。
5.ITサービスの導入・運用
DX化に必要な要件定義が済み、利用するサービスが決まったら、導入プロジェクトを進めていきます。社内のプロジェクトリーダーやシステム担当者、ベンダーなどと、密接にコミュニケーションを取ることが成功の秘訣です。
運用を開始する際は、現場の混乱をできるだけ避けるため、スモールスタートを意識することが大切です。小さな業務で成功例を積み上げ、次第に大きな業務へと適用していくとスムーズに進められます。
製造業におけるDXで失敗しないポイント
製造業のDX化で成果を挙げるためには、PDCAサイクルを回す仕組みを構築することが不可欠となります。単にIoT機器や管理システムを導入するだけでは、DXが実現されているとはいえないからです。
具体的には、データを収集・統合・分析するためのシステム構築や、現状をチェックし、改善していくための組織づくりが必要となるでしょう。システムと人がうまく協働することで、PDCAサイクルがうまく回るようになります。
最近ではPDCAのほかに、「Observe(観察)」「Orient(状況判断)」「Decide(意思決定)」「Act(行動)」からなる、「OODAループ」という概念も登場しました。これはアメリカ空軍の大佐によって提唱されたもので、PDCAよりも素早い意思決定が可能になるフレームワークです。
製造業がDX化を進めるにあたって、OODAループを用いて運用するやり方も、非常に効果的です。いずれにせよ、IT技術の導入後も、改善活動へ継続的に取り組み続ける姿勢が大切です。
製造業におけるDX化に成功した事例
ここでは、製造業におけるDX化に成功した事例を2つご紹介いたします。
株式会社アイデンの事例
株式会社アイデンは、制御盤や分電盤などを製造・販売する日本のメーカーです。
同社は、主力事業である制御盤の製造について、熟練工の知識や経験に依存していたため、作業の標準化がなされていない課題が発生していました。また、分業ができておらず、「一人の作業者がすべてを生産する」という事態も起こっていたのです。
そこで、CAD(Computer Aided Design)ベンダーと協力し、社内のDX化を推進。ジョブ管理システムを導入し、作業の標準化・分業化に取り組みました。
熟練工へは、より付加価値の高い業務に就いてもらうことで、理解を得ることに成功。設計部門の担当者を新しく採用し、育成することで、組織力の強化を図りました。
結果、製造工程が明確化され、作業の進捗を一元管理することが可能に。必要な部分を機械化することで、生産性を大幅に向上させたのです。
ダイキン株式会社の事例
ダイキン株式会社は、空調機や化学製品を手掛ける世界的なメーカーです。
同社は、近年の多様化する顧客のニーズにこたえるため、「マス・カスタマイゼーション」による低価格化・製品の差別化を模索していました。そこで、「工場IoTプラットフォーム」構想を掲げ、サプライチェーンの最適化、エンジニアリングチェーンの最適化、情報領域の最適化などを達成する目標を打ち立てたのです。
具体的には、大阪に新工場を設立し、すべての機械設備をネットワークでつなぐ取り組みを実施。データの発掘・収集・統合・一元把握などを容易にできるようにしました。
結果、同社の生産状況を一目で把握できるようになり、製造ロスの低減に成功。製造に関する予測や、判断基準のモデル化などが可能になったのです。
製造業においてもDXを進めて、業務を変革しよう
この記事では、製造業がDXへ取り組む重要性や現状、具体的な取り組みポイントなどについて解説しました。製品の製造が容易になった現代において、企業間の厳しい競争を勝ち抜くため、DX化は免れえない状況となっています。
業界全体では、まだまだDXへの取り組みが進んでいるとはいえない状況です。しかし、視点を変えて見れば、大きな業務改革を成し遂げたり、新たなビジネスチャンスを見つけ出したりする機会であるともいえます。
製造業がDXを進める際は、目的の明確化や、スモールスタートを意識することが失敗しない秘訣です。ぜひこの記事を参考に、自社のDX化を進めてみてください。